4.
IMMOBILISATION DES BORDS A SOUDER PAR POINTAGE
L'immobilisation
des bords à souder dans la position correcte peut se faire à
l'aide de points de soudure plus ou moins éloignés selon
que les tôles sont plus ou moins épaisses et que les parties
à assembler sont plus ou moins rigidement maintenues pendant le
soudage, cette opération prend le nom de "pointage".
Le
schéma 1923, représente le pointage sur tôle
plane rectangulaire, et le schéma 1924 représente
le "pointage" d'un fond sur virole.
Pour
le "pointage" des tôles d'acier planes et relativement
libres, on utilise en général la règle suivante :
- lorsque
l'épaisseur (e) est inférieure ou égale à
5 mm, on espace les points de 30 fois l'épaisseur (e).
- lorsque
l'épaisseur (e ) est supérieure à 5 mm, on
espace les points de 20 fois l'épaisseur (e).
Les
points de soudure sont exécutés autant que possible sans
métal d'apport pour les soudures bout à bout sur bords
droits. Pour les autres types d'assemblage, ils sont exécutés
avec métal d'apport, dans ce cas, l'apport du métal doit
être assez peu abondant pour ne pas créer de difficultés
de soudage, lors du passage des points, mais suffisant pour que les
points ne cassent pas. Lorsque la préparation est faite par chanfrein
en V, on a intérêt, si la tôle est accessible des
deux côtés, à exécuter les points à
l'envers.
Ainsi
pour pointer deux tôles rectangulaires schéma 1923,
on exécute les points dans l'ordre indiqué, en commençant
par le centre, la flamme du chalumeau étant toujours dirigée
vers l'extrémité libre des tôles.
Pour
le pointage des fonds de récipient sur les viroles schéma
1924, on exécute les points dans l'ordre indiqué.
Il
peut arriver que l'on soit amené à exécuter, au
lieu de points, des petits éléments de soudure dont la
résistance est suffisante pour s'opposer aux déformations
ou pour réaliser un véritable préassemblage permettant
de déplacer les pièces en vue de leur positionnement.
|
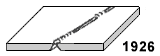 |
|
|
|
Ces
portions d'assemblages doivent cependant être assez peu chargées
et, dans ce but, exécutées avec le minimum de métal
d'apport, voire sans métal d'apport ; d'autre part, elles doivent
obligatoirement être pénétrées pour ne pas
créer de défauts dans la soudure finale, du fait de leur
présence, schémas 1925, 1926 et 1927.
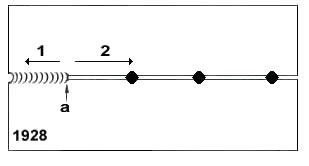
En
soudage à gauche, il n'est pas possible de commencer à
l'extrémité des tôles ; il est nécessaire
d'exécuter, au préalable, un petit cordon de soudure d'une
dizaine de cm, commençant en pleine tôle et se terminant
à l'extrémité schéma 1928, ce fragment
de soudure porte le nom de "talon", l'exécution
d'un "talon" n'est pas nécessaire lorsqu'on
utilise la méthode à droite ou la méthode à
double cordon.
5.
METHODES DE SOUDAGE DES ACIERS
Pour
exécuter des soudures dans les meilleures conditions de qualité,
de rapidité et d'économie, il convient d'appliquer des méthodes
éprouvées.
Ces
méthodes définissent, en fonction des positions de soudage,
du type d'assemblage et des épaisseurs à souder, la tenue
du chalumeau et de la baguette d'apport, les préparations et les
caractéristiques d'exécution.
5.1.
On distingue trois grandes classes de méthodes dans lesquelles
le soudage s'exécute de façon continue, c'est à
dire que le soudeur maintient un bain de fusion, de forme et de dimension
à peu près constante, et le déplace à vitesse
uniforme le long du joint, la partie arrière du bain de fusion,
en se solidifiant, engendre la soudure, ce sont :
- les
méthodes "à gauche" (ou "en
avant") dans lesquelles la flamme est dirigée
vers l'avant du bain de fusion, c'est à dire dans le sens
de progression.
- les
méthodes "à droite" (ou "en
arrière") dans lesquelles la flamme est dirigée
vers l'arrière du bain de fusion, c'est à dire en
sens inverse de la progression.
- les
méthodes "à double cordon"
dans lesquelles la (ou les) flamme(s), tout en étant dirigée
dans le sens de l'avance, assure la formation d'un bain de fusion,
à cheval sur l'épaisseur des tôles, de façon
à obtenir un cordon de soudure sur chaque face.
Les
différentes méthodes sont susceptibles de variantes selon
l'épaisseur des tôles, le type de joint et la position
de soudage.
5.2.
On peut distinguer sept positions fondamentales de soudage :
5.2.1. position à plat
- les tôles sont horizontales,
bout à bout et accessibles par la face supérieure, on
peut également assimiler à cette position, la position
"en toit" des soudures d'angle extérieure.
5.2.2.
position demi-montante - les tôles sont bout à bout
et légèrement inclinées sur l'horizontale, les
bords à souder suivant la ligne de la plus grande pente, on
peut assimiler à cette position, la position demi-montante
des soudures d'angle extérieur, dans laquelle les deux tôles
disposées en "toit" restent symétriques
l'une de l'autre par rapport à la verticale, mais l'arête
du toit est légèrement inclinée sur l'horizontale.
5.2.3.
position en gouttière
- soudures d'angle intéreur,
les deux tôles sont symétriques l'une de l'autre par
rapport à la verticale et la soudure est accessible par la
partie supéreure.
5.2.4.
position horizontale à plat - soudures
d'angle intérieur, l'une des tôles est horizontale et
la soudure est accessible par la face supéreure.
5.2.5.
position en corniche - les
tôles sont verticales bout à bout et la soudure horizontale
5.2.6.
position verticale - les
tôles et la soudure sont verticales (soudure bout à bout
ou soudure d'angle).
5.2.7.
position au plafond - les
tôles sont horizontales et accessibles par la face inférieure.
Quelle
que soit la méthode utilisée, certains principes doivent
être observés :
- l'extrémité
du métal d'apport doit rester pendant le soudage dans la zone
de la flamme qui le protège contre l'oxydation.
- le
chalumeau soudeur ne doit pas être relevé brusquement
en fin de soudure.
- chaque
arrêt en pleine soudure doit faire l'objet d'une reprise en
arrière (10 à 15 mm) assurant la fusion complète
de la fin du cordon précédent.
5.3. Soudage "à gauche"
Le
bec du chalumeau et le métal d'apport sont dans le plan de symétrie,
la flamme du chalumeau est dirigée dans le sens de l'avance et
le métal d'apport dans l'autre sens. L'avance du chalumeau est
uniforme tout le long du joint (pas de mouvements transversaux giratoires
ou semi-circulaires). L'extrémité du métal d'apport
reste dans la zone protégée (panache de la flamme) et
plonge par instants dans le bain, donnant ainsi la quantité de
métal apportée.
En
soudage au plafond, le chalumiste se trouve lui-même dans le plan
de symétrie du joint et de telle façon que la soudure
progresse en se rapprochant de lui.
Dans
les autres cas, le chalumiste est placé de telle façon
que la soudure progresse devant lui (de droite à gauche s'il
est droitier) .
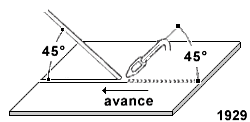
épaisseur
à souder en mm |
1
|
1,5
|
2
|
2,5
|
3
|
débit
du bec en l/h d'acétylène |
100
|
140
|
200
|
250
|
315
|
diamètre du métal d'apport en mm |
2
|
2
|
3
|
3
|
3
|
Le
schéma 1929, représente une position bout à
bout et un joint plat, bords relevés pour une épaisseur
inférieure à 1 mm, bords droits pour une épaisseur
comprise entre 8/10 et 3 mm , et une consommation d'acétylène
variable ~ de 100 à 120 l/h par mm d'épaisseur.

épaisseur
à souder en mm |
4
|
5
|
6
|
8
|
10
|
débit
du bec en l/h d'acétylène |
400
|
500
|
630
|
800
|
1000
|
diamètre du métal d'apport en mm |
3/4
|
3/4
|
4
|
5
|
6
|
Le
schéma 1930, représente une position bout à
bout demi-montante, bords droits pour une épaisseur comprise
entre 4 et 5 mm, chanfrein en V à 90° pour une épaisseur
comprise entre 5 et 10 mm, et une consommation d'acétylène
variable ~ de 100 à 120 l/h par mm d'épaisseur.

épaisseur
à souder en mm
|
1
|
2
|
3
|
débit
du bec en l/h d'acétylène
|
70
|
140
|
200
|
diamètre du métal d'apport en mm
|
1,5
|
2
|
3
|
Le
schéma 1931, représente d'une part une position
en angle extérieur à plat, chanfrein naturel à
90°, pour une épaisseur inférieure à 3 mm,
et une consommation d'acétylène ~ de 75 l/h par mm d'épaisseur.
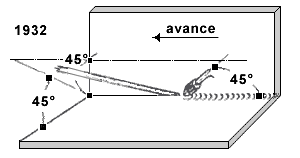
épaisseur
à souder en mm |
1
|
2
|
3
|
4
|
5
|
6
|
8
|
10
|
débit
du bec en l/h d'acétylène |
140
|
250
|
315
|
500
|
630
|
800
|
1000
|
1250
|
diamètre du métal d'apport en mm |
2
|
3
|
3
|
4
|
4
|
4
|
5
|
5
|
Le
schéma 1932, repésente une position en angle intérieur
horizontal, chanfrein naturel, pour une épaisseur comprise entre
1 et 5 mm, et une consommation d'acétylène variable ~
de 125 à 130 l/h par mm d'épaisseur.
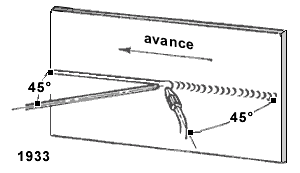
épaisseur
à souder en mm |
1
|
1,5
|
2
|
2,5
|
3
|
débit
du bec en l/h d'acétylène |
100
|
140
|
200
|
250
|
315
|
diamètre du métal d'apport en mm |
2
|
2
|
3
|
3
|
3
|
Le
schéma 1933, représente une position bout à
bout en corniche, bords droits, pourune épaisseur inférieure
à 5 mm, et une consommation d'acétylène ~ de 100
l/h par mm d'épaisseur.
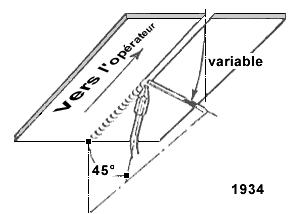
épaisseur
à souder en mm |
5
|
6
|
7
|
8
|
10
|
débit
du bec en l/h d'acétylène |
315
|
400
|
500
|
630
|
800
|
diamètre du métal d'apport en mm |
3
|
3
|
3
|
4
|
4
|
Le
schéma 1934, représente une position bout à
bout au plafond, bords droits, pour une épaisseur inférieure
à 5 mm, et une consommation d'acétylène ~ de 70
l/h par mm d'épaisseur, et chanfrein en V de 70° à
80° pour une épaisseur comprise de 5 à 10 mm, et une
consommation d'acétylène ~ de 75 l/h par mm d'épaisseur.
5.4.
Soudage "à droite"
Bec
du chalumeau et métal d'apport sont dans le plan de symétrie,
la flamme est dirigée en sens inverse de l'avance, et le métal
d'apport dans le sens d'avance.
Le
chalumiste fait progresser la soudure de sa gauche vers sa droite (s'il
est droitier), l'angle que fait le chalumeau avec la soudure varie de
40° à 70°, tout en étant animé d'un mouvement
de translation uniforme dans le plan de symétrie.
Le
métal d'apport plonge dans le bain de fusion et est animé
de mouvements transversaux.
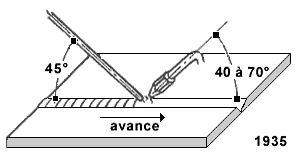
épaisseur
à souder en mm |
5
|
6
|
8
|
10
|
12
|
débit
du bec en l/h d'acétylène |
500
|
630
|
800
|
1000
|
1250
|
diamètre du métal d'apport en mm |
3
|
3
|
4
|
5
|
6
|
Le
schéma 1935, représente une position bout à
bout et à plat, pour une épaisseur comprise de 5 à
12 mm, et chanfrein en V à 70°, et une consommation d'acétylène
~ de 100 l/h par mm d'épaisseur.
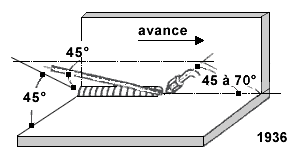
Le
schéma 1936, représente une position en angle intérieur
horizontale, pour une épaisseur comprise de 6 à 10 mm,
et chanfrein naturel, et une consommation d'acétylène
~ de 120 l/h par mm d'épaisseur.
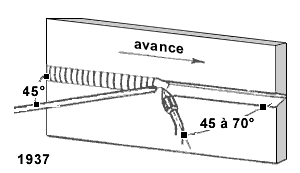
Le
schéma 1937, représente une position bout à
bout en corniche, pour une épaisseur comprise de 6 à 12
mm, et chanfrein en V à 70°, et une consommation d'acétylène
~ de 70 l/h par mm d'épaisseur.
5.5.
Soudage "à double cordon"
Le
bec du chalumeau et le métal d'apport sont dans le plan de symétrie.
La flamme du chalumeau est dirigée dans le sens de l'avance et
fait avec la soudure un angle de 45°. La pointe du dard est au maximum
à 1 mm du bain de fusion, le métal d'apport est incliné
en sens inverse de l'avance, et fait avec les bords à souder
un angle de 45°.
Le
mouvement du chalumeau est rectiligne et uniforme, l'extrémité
du métal d'apport reste protégé par le panache
de la flamme et plonge par instants dans le bain de fusion en exécutant
de petits mouvements transversaux destinés répartir le
métal fondu.
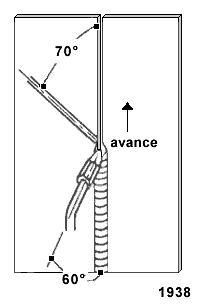
épaisseur
à souder en mm |
2
|
3
|
4
|
5
|
6
|
débit
du bec en l/h d'acétylène |
100
|
200
|
250
|
315
|
400
|
diamètre du métal d'apport en mm |
2
|
2
|
2
|
3
|
3
|
Le
schéma 1938, représente une position bout
à bout ou en angle extérieur vertical en montant, bords
droits, d'une part pour une épaisseur comprise de 2 à
6 mm, et une consommation d'acétylène ~ de 60 l/h par
mm d'épaisseur, et d'autre part pour une épaisseur comprise
de 7 à 10 mm, chanfrein en V à 90°, et une consommation
d'acétylène ~ de 60 l/h par mm d'épaisseur.
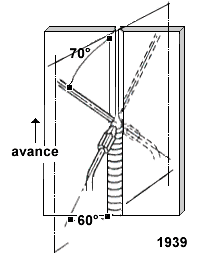
épaisseur
à souder en mm |
3
|
4
|
5
|
6
|
7
|
8
|
10
|
12
|
14
|
16
|
18
|
20
|
débit
du bec en l/h d'acétylène |
70
|
100
|
140
|
140
|
200
|
250
|
315
|
400
|
400
|
500
|
500
|
630
|
diamètre du métal d'apport en mm |
2
|
2
|
2
|
3
|
3
|
3
|
3
|
3
|
4
|
4
|
4
|
4
|
Le
schéma 1939, représente une position bout à
bout ou en angle vertical en montant, bords droits, d'une part pour
une épaisseur comprise de 3 à 10 mm, et une consommation
d'acétylène ~ de 30 l/h par mm d'épaisseur, et
d'autre part pour une épaisseur comprise de 12 à 20 mm,
chanfrein en X à 80°, et une consommation d'acétylène
~ de 30 l/h par mm d'épaisseur.
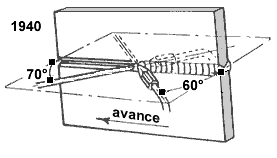
Le
schéma 1940, représente une position bout
à bout en corniche, pour une épaisseur comprise de 6 à
12 mm, chanfrein en X à 80°, et une consommation d'acétylène
~ de 30 l/h par mm d'épaisseur.
5.6.
Soudage par bains successifs (en deux temps)
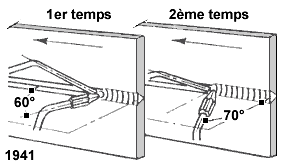
épaisseur
à souder en mm |
5
|
6
|
8
|
10
|
12
|
15
|
débit
du bec en l/h d'acétylène |
315
|
400
|
500
|
630
|
800
|
1000
|
diamètre du métal d'apport en mm |
3
|
3
|
3
|
4
|
4
|
4
|
Le
schéma 1941, représente une position bout
à bout en corniche, pour une épaisseur supérieure
à 5 mm, chanfrein en V à 70°, et une consommation
d'acétylène ~ de 75 l/h par mm d'épaisseur.
pages
| 1 | 2 | 3
|
|